Presentamos un proceso de industrialización que asegura módulos de baterías más eficientes
Fabricar baterías más eficientes es el reto. El gran reto. La forma de las pilas y su composición química, la disposición en los módulos, la refrigeración… son muchos los elementos que determinan que el producto final pueda ofrecer los resultados requeridos. Y uno de los más importantes es la materialización de los módulos. Para este desafío, en Industrias Alegre tenemos ya lista una propuesta de máxima precisión. ¿Quieres conocerla?
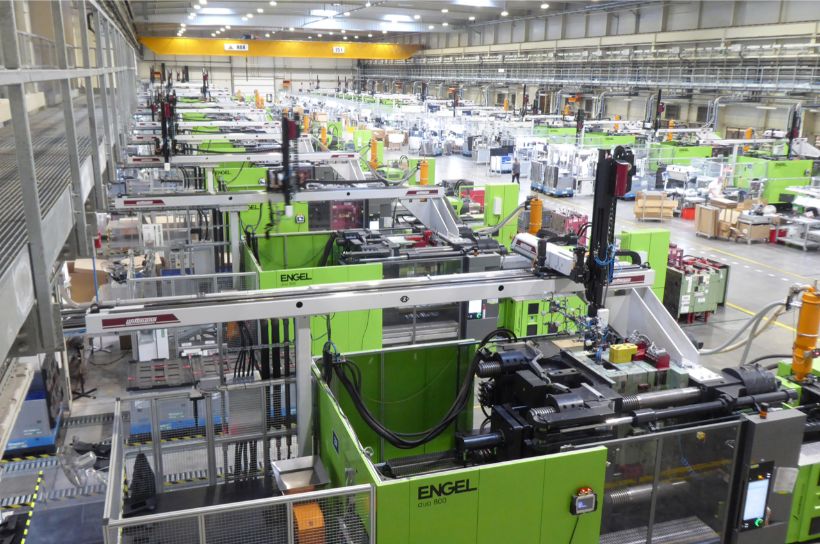
En la movilidad eléctrica, las baterías son mucho más que acumuladores de energía: son la base del rendimiento de los nuevos vehículos. Y, dentro de las baterías, los módulos que las componen son mucho más que un mero ensamblaje físico: son el elemento del que depende la escalabilidad y la gestión eficiente de la energía.
Por eso no vale cualquier módulo. Para que esta pieza contribuya a obtener una batería de alto rendimiento, su fabricación debe ser extraordinariamente precisa. Y eso es lo que ahora propone Industrias Alegre al mercado de la electrificación y las baterías: un proceso que contribuye a mejorar su eficiencia, su capacidad de carga y su durabilidad.
De la investigación a la propuesta comercial
En Industrias Alegre nos adentramos en la realidad de las baterías con DETEBAT-VE, a mediados de 2021, una investigación colaborativa que buscaba desarrollar una batería eficiente capaz de superar las exigencias de la normativa europea 2030 y que estuvo liderado por el Instituto CMT - Clean Mobility & Thermofluids de la (UPV). “En este proyecto nos ocupamos del diseño de los módulos y para ello utilizamos piezas de polipropileno fabricadas en impresora 3D, lo que nos permitió ir ajustando los diseños hasta lograr el mejor”, nos comenta José Pérez, ingeniero de nuestro equipo de I+D+i (tienes más detalles del proyecto en este enlace). Esta investigación permitió a nuestros expertos conocer en detalle todos los requerimientos exigibles a los módulos, que son muchos.
Y con estos aprendizajes, el siguiente paso consistió en abordar técnicamente esta pieza, pero ahora pensando ya en su industrialización a gran escala. “Para ello ha sido necesario estudiar diversas propuestas de diseño y de proceso, enfrentando problemas diversos. Hemos buscado y descartado soluciones hasta dar con la que consideramos más adecuada”, dice Miguel Alagarda, director técnico de Industria Alegre.
Sobreinyección de aluminio con resultados de alta fiabilidad
La propuesta que hoy tenemos sobre la mesa está pensada para celdas cilíndricas. Es cierto que en el mercado hay otras propuestas (tipo prismáticas o tipo pouch) y que las preferencias pueden variar más adelante, pero hoy por hoy esta es la opción que han elegido los líderes mundiales de vehículos eléctricos, con Tesla y Lucid a la cabeza. Y para estas celdas se ha propuesto un módulo de plástico reforzado con sobreinyección de insertos de aluminio. Esta pieza en forma de cesta, en la que encajan las celdas cilíndricas, debe ofrecer una gran resistencia mecánica, evitar los rozamientos y asegurar una buena disipación térmica. Todo ello, con el menor peso posible.
Pero la sobreinyección de esta pieza no es fácil, según nos explica Alagarda. “La primera cuestión —explica el director técnico de Alegre— es que debemos fabricar el módulo completo de una sola inyectada y conseguir que la parte inferior se presente completamente limpia de polímero, sin ningún tipo de filtraciones”. Esta no es una cuestión baladí porque es en esa cara exterior donde se sitúan las conexiones de los módulos entre sí y con el paquete de baterías. De esa limpieza en la inyección dependerá que el rendimiento del conjunto sea el esperado.
Inyectar en vertical y asegurar una inyección perfecta
El segundo desafío productivo es el que supone trabajar con unos insertos de aluminio que no se pueden imantar. “Esta situación podríamos resolverla con elementos de succión. Lo hacemos en muchos otros casos. Pero en esta ocasión corremos el riesgo de obtener unos resultados menos precisos o que haya pequeñas desviaciones en la planitud de la base. Y ese es un riesgo que no queremos asumir porque la más mínima desviación vuelve a redundar en la eficiencia final de la batería”.
¿La propuesta realizada desde Industrias Alegre? Apostar por la inyección en vertical. “Sí —continúa Alagarda— es una forma de inyectar menos convencional que además implica contar con una maquinaria prácticamente a medida, montada especialmente para nosotros. Pero es el modo de producir piezas con la calidad requerida”.
Tras la inyección, el último paso es el de asegurar el aislamiento en la unión entre plástico y aluminio, para evitar que se creen arcos eléctricos o derivaciones que constituyan un riesgo de seguridad en el módulo. El experto ingeniero continúa con su explicación: “Realizamos una soldadura de 90 puntos a cada uno de los módulos para evitar los riesgos mencionados que resulta crítica también para la eficiencia de la batería. En este caso, el reto mayor ha sido diseñar un proceso de soldadura con la precisión necesaria y control de parámetros punto a punto para garantizar la calidad de la pieza final”.
Proceso listo para industrializar
Sobreinyección en vertical, soldadura controlada, planitud asegurada. No ha sido sencillo, pero ya podemos ofrecer al mercado ese proceso de fabricación de alta precisión que la nueva movilidad está demandando.
Porque la industrialización de las baterías está despegando y abriéndose paso hacia el futuro. Y en Industrias Alegre queremos formar parte de este porvenir apasionante.