Fabricación aditiva en polipropileno: una realidad a pleno rendimiento
Fuimos la primera firma española y una de las pocas europeas que apostó por esta tecnología en cuanto HP la puso en el mercado, hace algo más de un año. El aprendizaje ha sido duro. Pero hoy nuestra sección 3D está a pleno rendimiento: cada vez más compañías disfrutan de las ventajas de pasar de la idea a la pieza real en un tiempo récord.
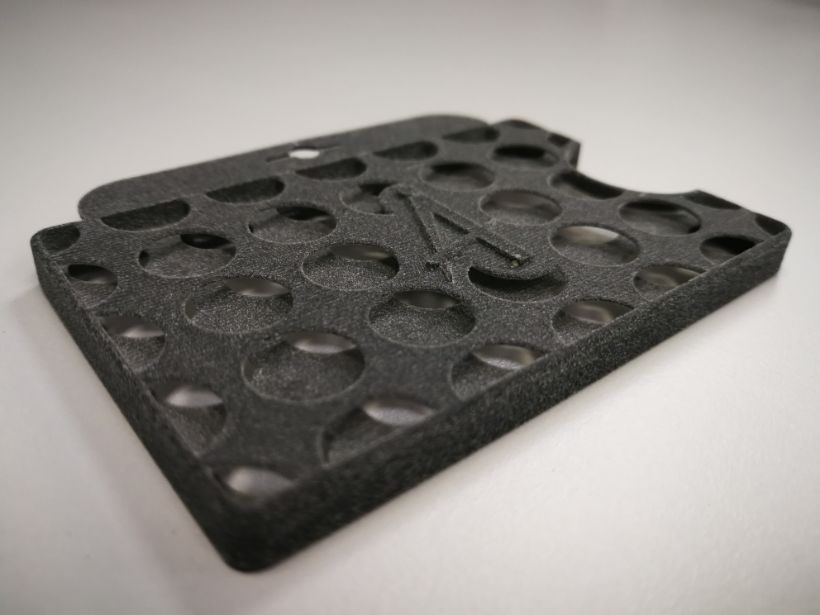
Nuestra sección dedicada a la fabricación aditiva lleva pocos meses en marcha, pero vive una actividad constante. Ya se han hecho habituales los encargos para realizar preseries, prototipos y proyectos destinados a validar cambios en el diseño de piezas.
Acelerar la innovación
La demanda, hasta el momento, está protagonizada por la industria más competitiva y por diversos organismos dedicados a la investigación. Y es que, para este tipo de equipos profesionales, la impresión 3D con polipropileno supone contar con respuestas reales y rápidas. “Gracias a esta tecnología –comenta Amparo Vázquez, nuestra directora de I+D+i– se pueden proponer soluciones, explorar modificaciones y validar cambios teniendo las piezas en la mano y recorriendo todo el ciclo brevemente. Lo que estamos ofreciendo a otras industrias es la capacidad de acelerar sus procesos de innovación para hacerse más competitivas”.
Más allá de los prototipos
Pero las posibilidades de la tecnología aditiva van mucho más allá de la validación de piezas o de los prototipos. Porque, después de todo, estamos trabajando con polipropileno, un polímero que, en esta tecnología Multi Jet Fusion de HP, tiene las mismas características que en inyección: es resistente a los químicos, soldable, con baja absorción de humedad y capaz de ofrecer piezas funcionales.
Por eso la demanda de nuestra joven sección 3D comienza a ampliarse dentro y fuera del sector de la automoción, con encargos de utillajes, repuestos y piezas personalizadas.
“Trabajar con fabricación aditiva implica grandes ventajas”, comenta de nuevo la responsable de innovación, que señala, concretamente tres aspectos:
- Podemos realizar morfologías que resultan imposibles en inyección.
- Conseguimos piezas más ligeras que las tradicionales.
- Podemos conseguir piezas complejas que, de otro modo, necesitarían montaje.
Un servicio completo
Pero ¿cómo abordar un proyecto que se resuelve con fabricación aditiva? Para nuestra compañera Mónica Alegre, responsable del área comercial, la respuesta es simple: “igual que tratamos los proyectos para inyección, aplicando una filosofía full supply”. Y explica: “aportamos nuestro know how en todo el proyecto y lo ponemos a disposición del cliente desde el estudio previo a la pieza final; aunque también ofrecemos otras ventajas, como la de adquirir cubas completas de material para rebajar precios, atender pedidos urgentes o realizar servicios personalizados”. Sencillo, rápido y, sobre todo, muy eficaz.