Electrification comes to bicycles with Spiny and our additive manufacturing
From conventional to electric bicycle in just 5 seconds. This is what Spiny, the start-up that is revolutionizing the way of understanding urban pedaling, offers. Because it is no longer necessary to have a team to go out on the weekend to sweat the shirt and another to go to work comfortably and arrive with an impeccable appearance. Spiny lets you electrify your bike when you need it. And in this project, our additive manufacturing plays a major role.
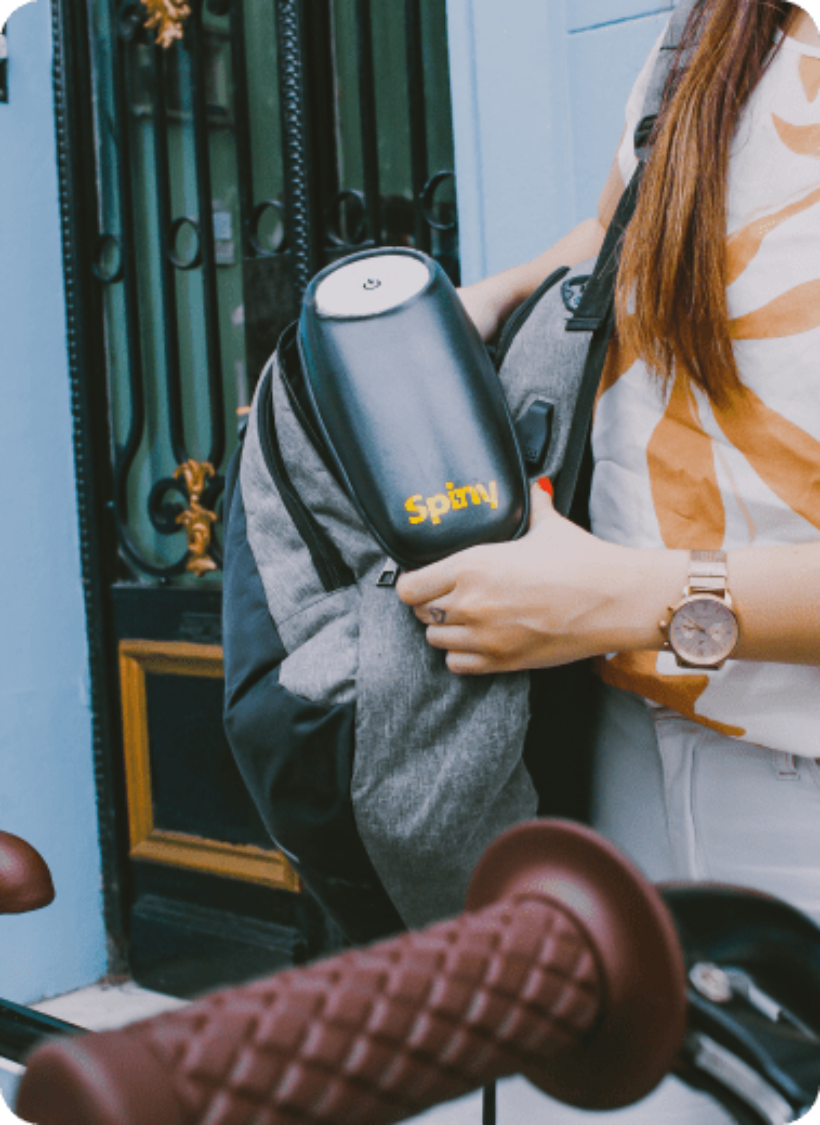
The newly released device offers a high efficiency motor with 250W, a range of up to 40km and a speed of up to 25km/h. These features and the fact that it can be removed and put on so quickly has already started to make bike lovers fall in love with it. Yes, Spiny is a product of undoubted wow effect. But to get to this point, its creators have sweated more than when they were out pedaling together for pure pleasure. Industrial innovation is a long, hard road.
"When we launched the idea, all three partners were involved in the development of the company and we did the whole initial process on our own, without external financial investment," says Marco Cocchiarella, one of the founders. "Of course we had an engineering team, but innovation in industry is a process that takes a long time, requires many checks and very costly processes until we have a viable product ready to launch on the market. That's where we came into contact with Industrias Alegre.
ADDITIVE TO VALIDATE THE DESIGN...
When they were in the development and validation phase of their product, Spiny's managers met Industrias Alegre during a Mobility Innovation Valencia and that was the start of a very satisfactory collaboration between the two companies. A collaboration that, within Alegre, has been led by Enri Llorens and Manuel Casasús, from our additive manufacturing section.
"We had already seen that having 3D printing in polypropylene can greatly accelerate the validation phase of any project," says Casasús, "and in this case, that moment has been especially fast because the initial test we did was quite successful. With it we were able to confirm the details of the product and the geometry of the mold that can be used when Spiny scales up its production, but it also served to confirm the material feasibility of the product using a polypropylene that will behave in the same way as when the time comes to inject the part".
...AND TO CONFIRM THE MARKET'S REACTION.
For Spiny's managers, the meeting with Industrias Alegre and additive manufacturing in polypropylene was very relevant because it involved validating prototypes, of course, but "the important thing is that it has allowed us to perform a market validation," Cocchiarella comments. He continues: "Producing the first units using 3D printing has allowed us to bring the product to the market and sell it without having to go into mass production beforehand, incurring large investments. It was crucial for us to know how the market was receiving our proposal. And not by using prototypes, but in a professional way, already offering a model identical to the one we will have when we can reach full-scale production."
A REWARDING PROJECT FOR BOTH PARTIES
When talking about this collaboration, smiles are on the faces of the protagonists of the two companies. It has been a very rewarding job. Llorens comments that, for the Alegre team, "it was like going back to the origins of our company and being with a client who can make decisions in a matter of minutes. In addition to focusing on one of our company's objectives, which is to provide competitive solutions for electric mobility". For Cocchiarella, on the other hand, it meant meeting "with an openness that I have rarely seen and that we did not expect since they are such a big industry compared to us".
And the fact is that the collaboration has extended beyond the validation and development of parts. Alegre has guided this start-up through a space through which the company usually travels, ensuring, thanks to his know-how, that the newcomers quickly found agile solutions and reliable suppliers that have complemented their industrial process. The entrepreneur sums it up: "They are a large industry with the heart of a microenterprise".