In the race for the best automotive battery, additive manufacturing has proven its great value
If there is urgency, additive manufacturing has a lot to contribute. And this has been demonstrated by our 3D team throughout DETEBAT-VE, a collaborative project in search of the cleanest battery led by the CMT Institute - Clean Mobility & Thermofluids of the Universitat Politècnica de València (UPV).
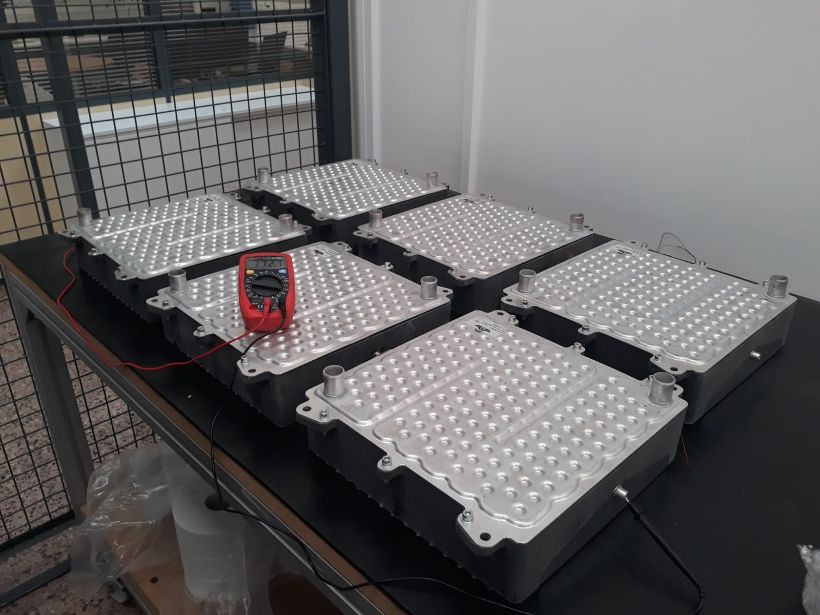
The automotive industry is currently in a race to find the most efficient and sustainable batteries, produced on the largest possible scale. And, in this context, the collaborative research project DETEBAT-VE has been developed, a work whose objective was to manufacture a demonstrator through which we could find a good battery model, which would be efficient and would have the minimum possible environmental impact throughout its useful life. The research involved many participants, each of whom contributed specific knowledge in one area.
"We were in charge of the modules, the container parts inside which the cells and sensors are incorporated, and which are attached to the cooling plate," says José Pérez, an engineer in our R&D&I department. And he continues: "The modules are elements that were traditionally manufactured in iron and were later lightened using aluminum. We have used polypropylene, which provides the required physical characteristics and with which we achieve a lightening of 40 to 50% with respect to aluminum".
Additive manufacturing as a shortcut
We know that, when it comes to mass production, the modules would be manufactured in plastic injection molding, which is always more cost-effective for long runs. But with research underway, additive manufacturing was a valuable shortcut, allowing us to produce successive functional prototypes in as little as two or three days. No molds. No waiting.
"The biggest challenge of the project for our company was to come up with the best design for the part while also making it meet the many physical requirements," says Perez. In this sense, 3D printing has been crucial, "because we have been able to make small adaptations to the design and, once it has been definitively defined, we have been able to have prototypes on which we have carried out the necessary tests, both mechanical and thermal, since the fact that it works as a flame retardant is one of the key requirements in the field of batteries.
Let the exchange of ideas flow
Being able to get the part into the lab to test it knowing that this prototype has the same functional characteristics as the part that, in the future, may be manufactured by injection molding, has been an essential advantage in the research process. Incorporating this manufacturing method," says Pérez, "brings agility and simplicity to the research. And, in this way, it allows the exchange of ideas and knowledge within the team to flow better". In fact, no one on the team today can imagine what it would have meant to have to wait several weeks for an injection mold before being able to carry out verifications.
This has been our experience with batteries. And you, what research are you developing? Would you like to have functional prototypes in record time?