“It’s not just about practicality, by avoiding lost containers we are also able to reduce our carbon footprint”
Smart HybridBoxes can be programmed to completely different projects, as every company has its requirements and every organisation has its own priorities. This is why our IoT container system is tailor-made to suit the needs of every client. Behind this customisation are Lourdes Solares, from the R+D+i department, and Jesús Ibáñez, Key Account Manager of the business unit. We spoke to them about the launch of this technology that made smart logistics a reality.
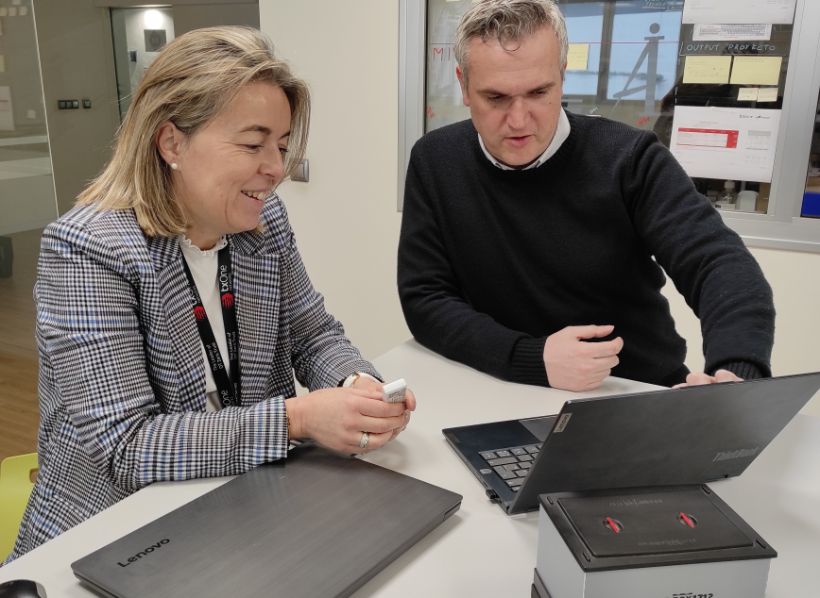
– Question: There are many advantages to IoT containers, but you emphasise the fact that it prevents losses. Does that much material really get lost?
– Lourdes Solares: We studied various automotive projects and we realised that the average percentage of lost containers was around 15% in each project. These losses don’t just happen when production is at a maximum and the containers are continuously rotating, when you most need them, they also happen when there isn’t much going around and they get stuck on one of the different floors on the circuit or random places.
– Jesús Ibáñez: These are our calculations. But recently, a TIER 1 shared an even more surprising figure. According to their study, up to 20% or even 25% of containers can get lost over the course of a project, equalling 7 mega trucks lost per project.
– Q: But these materials can’t just disappear...
– J. I.: They are considered lost once nobody knows where they are. What happens next is even worse, because they are taking up space in a supplier’s field or another warehouse and can’t be retrieved when they are needed.
– L. S.: In an efficient industry such as the automotive industry, these figures represent a serious attack on sustainability. It’s not just about practicality, by avoiding lost containers we are also able to reduce our carbon footprint
– Q: Has the sector not been able to find any solutions before now?
– J. I.: The industrial logistics sector has spent a long time optimising protocols and information systems to avoid such losses. In fact, many places use RFID technology to have some sort of control over their container fleet, but the information provided by radiofrequency is much more limited as it only sends a signal when it passes a certain point.
– L. S.: Anyone who works in the automotive sector knows that we usually use a day where there’s no activity (a holiday) to take inventory.
– Q: So this IoT system can locate a container at any time?
– L. S.: Yes. We have been running pilot tests for some time with a success rate that even we did not believe was possible. We experienced something very interesting during these tests. We sent a connected container to Barcelona and the transport agency got mixed up. The system told us that the container had arrived in Barcelona... but then it kept travelling towards the border and finally ended up in Toulouse in France. We thought the system was broken and we were looking for the error... Then we realised it was the transport company who made a mistake. This proved to us that the system really was reliable. If we had have trusted their data, we would have been able to solve the problem in record time.
– Q: Does it also work on long distances?
– J. I.: Yes, it works perfectly on long distances. We noticed that there were some precision errors on short distances at the start, but we know this can be easily fixed with prior mapping.
– Q: Is this system designed exclusively for the automotive sector?
– J. I.: No, but we are starting with this industry because we know it inside out - we are part of it. The sector is working hard to reduce its carbon footprint, so our proposal has extra value for its sustainability as it reduces material losses to zero.
– L. S.: Our connected containers are currently prepared to indicate their location and whether they are open, closed, empty or full. This is all an automotive company needs to know to manage its fleets. In other areas, we could offer information on a container’s weight, temperature, moisture level or vibration level. The information can be extensive and very valuable in the food, pharmaceutical, cosmetics and many other industries.
– J. I.: With these capacities, we are definitely going to open our system to other equally-demanding sectors.
– Q: How does a company specialised in plastics end up in connected logistics?
– J. I.: Industrias Alegre has extensive experience with containers in difference fields and our HybridBox design had already revolutionised logistics for circular loops. We have combined this knowledge with that of our technology partners to produce a reliable, high-impact, digital product,
– L. S.: Our involvement in the Audere project was very helpful. We worked with robotics and digitalisation experts who helped us see clearly how much each partner’s know how enriches the others and really speeds up innovation.